If you have ever been concerned about optimizing your work processes and increasing your productivity, or that of your team, you have surely heard the term Kanban.
But what does this word really mean? Is it a method? Is it complicated to use? How long does it take?
Don't worry, because these and other questions will be answered throughout this article! Stay with us!
What is Kanban?
Kanban is a Work Management Method in which it is possible to visualize the entire process workflow, as well as each individual activity that composes it, allowing the identification of bottlenecks and optimizing the flow as a whole.
In this regard, the main objective of Kanban is to Improve productivity of a process by avoiding the overload or idleness of teams.
Kanban has become a very popular tool in software development, but it is currently used by many companies in different markets. What you may not know is that this method was initially developed for the automotive industry.
A brief history
In the 1940s the Japanese car manufacturer Toyota was losing in terms of productivity and efficiency to its American competitors. This situation prompted Taiichi Ohno to develop the Kanban system, inspired by how supermarkets managed their stock and products on the shelves.
The idea was that automobile production was Pulled by Demand, meaning that stock levels were always aligned with production needs. In this way, communication happened as follows:
- People working on the shop floor communicated stock levels via a kanban* (Card);
- If the stocks were empty, the kanban communicated to the warehouses that a certain part should be replenished;
- The warehouse, in turn, passed the need on to the suppliers, who supplied the stocks with the necessary materials.
This process of optimized production originated the method we know today as Just-In-Time manufacturing.
* Kanban is a Japanese word that means “poster” or “visual board”. When we refer to the word, the first letter is spelled in lowercase (kanban). When we refer to the methodology, the first letter is capitalized (Kanban).
Taiichi Ohno created the Kanban method for the industrial process, but it was the American David J. Anderson Who adapted it for software development and released the book Kanban: Successful Evolutionary Change for Your Technology Business.
Today, Kanban is widely used to optimize workflows and improve the productivity of teams in various markets, areas, and types of companies.
Reading tip: Product Discovery: Identifying Problems and Defining Solutions
How to use Kanban?
As we will see later, Kanban is a method that requires no adaptations to get started.
So you can start using Kanban almost instantly, depending on the size of your team.
With visuals as one of its characteristics, the first thing to understand about Kanban is that it is necessarily a framework.
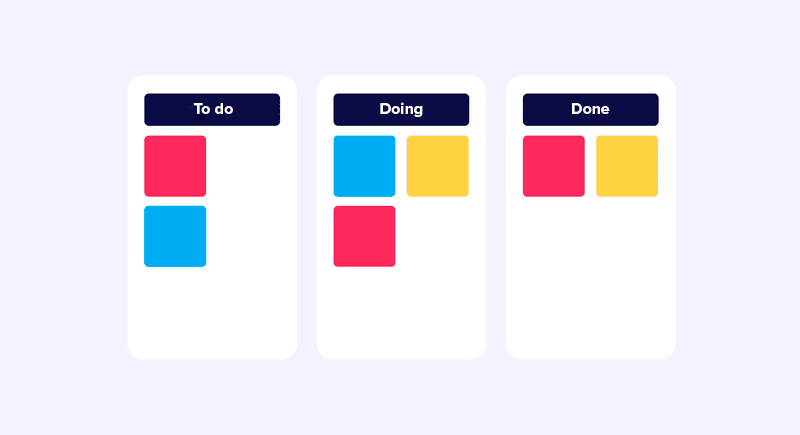
Above is an example of the simplest Kanban board that can be used. Each column indicates the statuses of each activity:
- To do: is the backlog of activities, that is, these are the tasks that have not yet been started;
- Doing: These are the tasks that are actually being performed at the moment;
- Donate: these are all the activities that have been completed.
From this example, we can explain the other elements that exist in a Kanban board. David J. Anderson lists the 5 fundamental elements of Kanban:
1) Visual elements
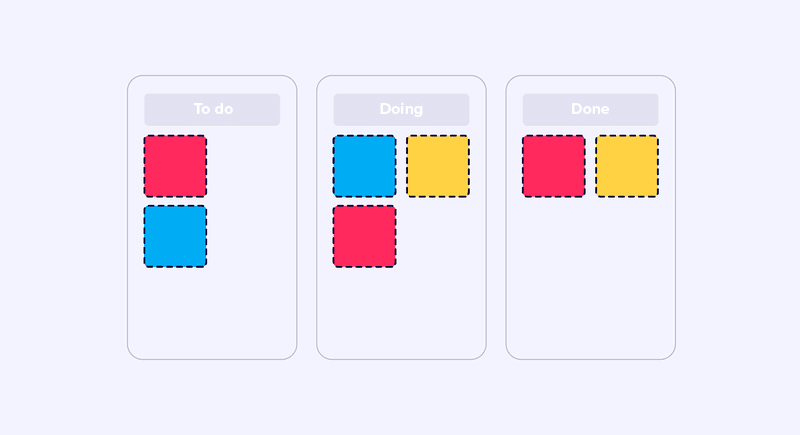
The first thing you may notice when looking at a Kanban board are the visual elements, such as cards, post-its, colored papers, and stickers. These can help you quickly identify tasks and progress within your workflow.
Each visual element usually corresponds to an activity within the workflow as a whole.
Besides the representational issue, visual elements allow easy identification of the status of activities, and if there are any bottlenecks or improvement opportunities that can be quickly resolved.
2) Columns
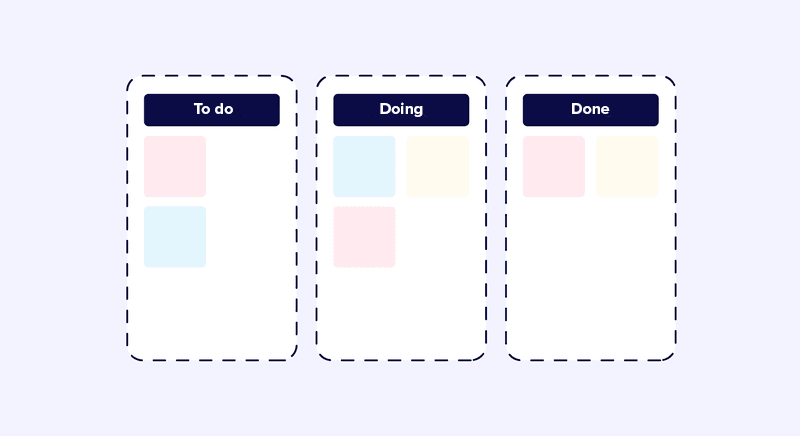
Columns are another present and fundamental characteristic of the Kanban boards.
In the example above we see 3 columns, but depending on the area or the type of process, there may be more (and usually there are).
Each column can represent a specific status (as in the example), an area of the company, or an activity as well.
The columns together form a Workflow in which the cards move from left to right through the columns until the tasks are completed.
This flow is the heart and soul of the Kanban method. In the example above, when an activity moves from “To Do” status to “Doing” status, visually anyone looking at the board knows what is being done and what is still in the queue.
Similarly, when the activity is finished, it is clear to everyone that the process of that task has come to an end.
3) Work-In-Progress (WIP) Limit
The WIP limit works more as a practice than an element of the Kanban framework itself, and we will cover it in detail later in the text.
But in general, limiting Work-In-Progress means Setting a Limit of Cards for each column so as not to overload the work of the people involved in the process.
4) Commitment Point
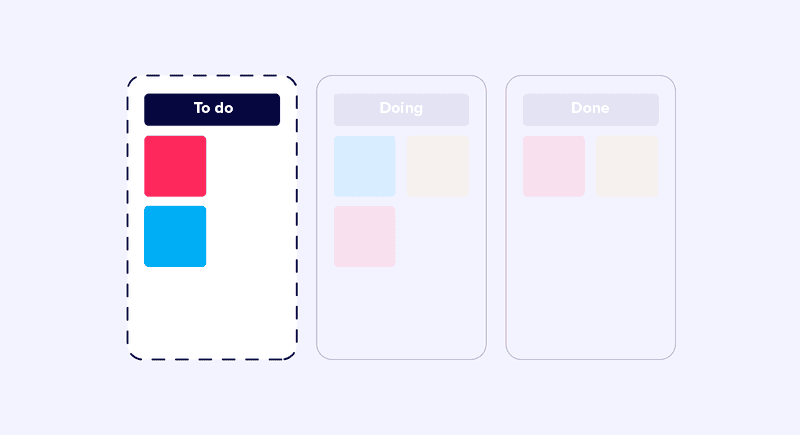
Anderson calls the commitment point a column for the Backlog of Ideas, activities, and tasks.
In the case of the example at the beginning of this section, the commitment point is the “To Do” column.
The idea is that the tasks placed in this column are pulled into the flow as soon as the previous task is finished.
The commitment happens because this movement is proactive, the team members themselves pull the task without needing someone (superior) to address them.
5) Delivery point
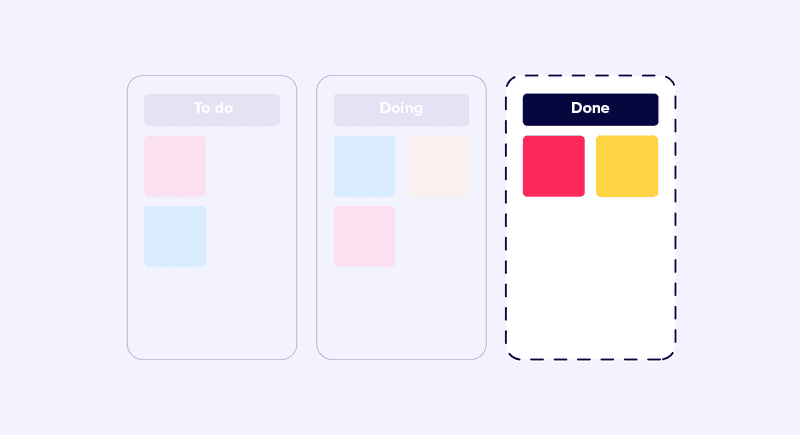
The delivery point is the column for Allocating the finished tasks, in the case of our example, the “Done” column represents this element.
Determining when a task is finished is important to be able to estimate its Lead time (the time it took to deliver the task) and also to create a sense of “job done” for the team, creating a certain motivation and well-being.
Taking these elements into consideration, you have what you need to build and start an initial Kanban board. As we said, Kanban boards vary depending on the area, process, and company.
Ideally, you should start with something simple, and as the team gets used to the method, they will suggest improvements and the inclusion of new columns to optimize the process.
Reading tip: Why Are Balanced Teams So Important To UX?
Digital and physical Kanban board
The main characteristic of Kanban is the construction of a visual representation of the workflow, in the form of a board with columns.
It is worth noting that the board can be either physical or digital.
In the past, it was common to build the boards on blackboards, Flipcharts, or even white walls. In fact, this practice may still hold true in some companies or teams.
But as Kanban and technology have become more popular, there are now programs that provide virtual boards for teams, such as Trello, for example.
One of the main advantages of using digital boards is the ease of adding columns, tasks, and the ability to collaborate with Remote Teams. These tasks are practically impossible with physical boards.
Examples of Kanban boards
The example above is a very simple one, containing only 3 columns.
However, the boards can be adapted to any process area, regardless of the area or market in which the company operates. The Trello tool gives some examples of Kanban boards, such as:
Publishing articles or content
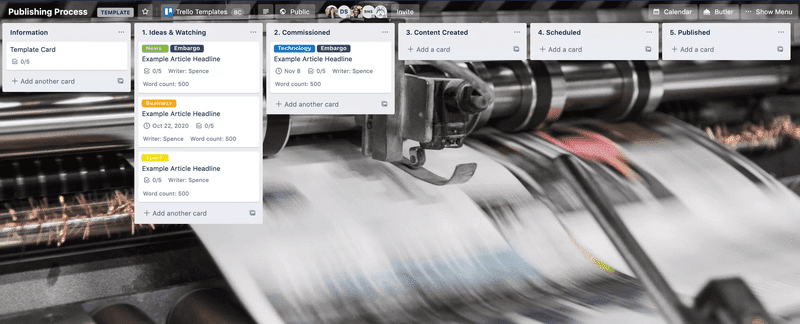
Project planning
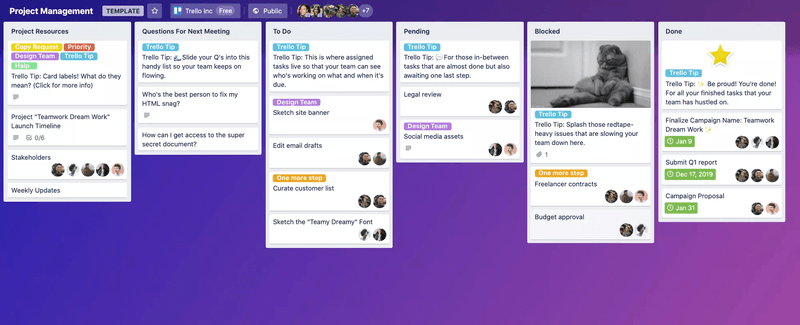
Sales flow
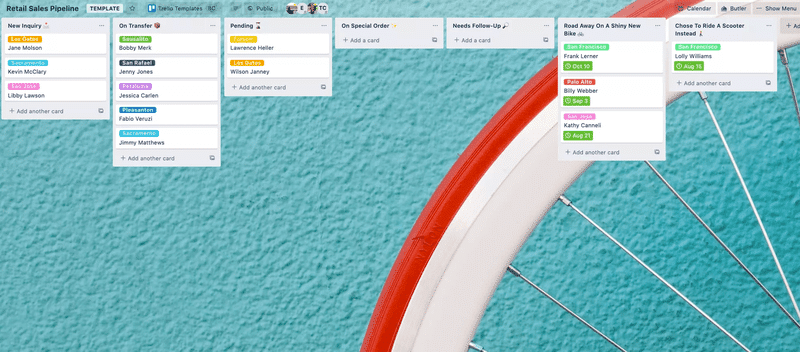
Trip planning
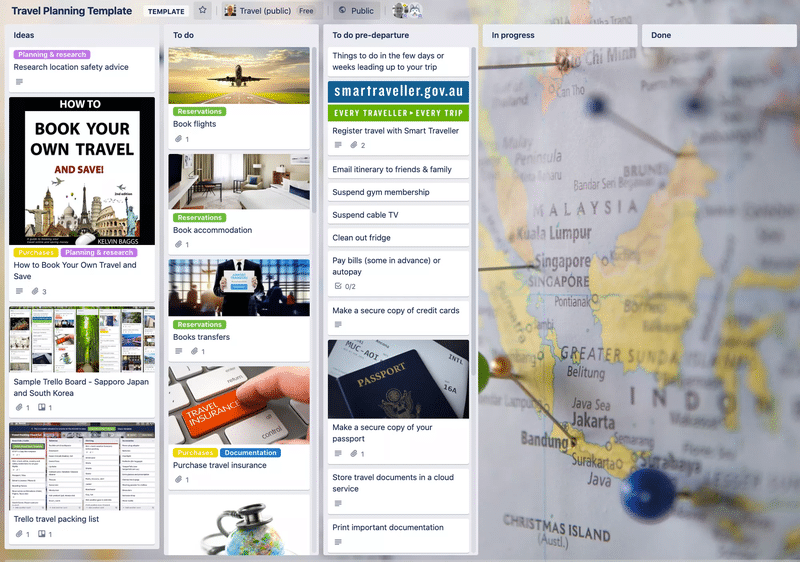
The interesting thing is that Kanban works to manage almost any process, even for your personal life.
Kanban principles and practices
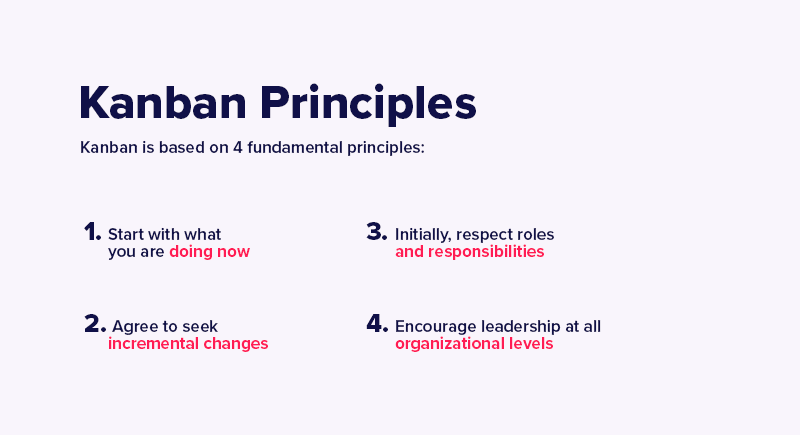
Kanban is based on 4 fundamental principles:
- Start with what you are doing now;
- Agree to seek incremental change;
- Initially, respect roles and responsibilities;
- Encourage leadership at all levels.
1) Start with what you are doing now
To start using Kanban in your workflow you don't need to make any changes or adaptations. You simply have to start using it.
This is possible because this method is simple and flexible, and can be implemented instantly in any area or company, without impacting the structures or culture of the organization.
As time goes by, Kanban will show where the bottlenecks in the process are and, this way, it is possible to solve the problems and Improve productivity of the teams.
2) Agree to seek incremental changes
The idea of Kanban is not to promote radical and disruptive changes overnight. So much so that its implementation is practically instantaneous because it does not promote initial friction.
As time goes by, productivity problems are identified, and thus Can the team propose small incremental and evolutionary changes to improve the process.
This process of change little by little reduces people's fears and uncertainties and begins to encourage small ideas and opportunities for improvement.
3) Initially respect roles and responsibilities
Again, because it is a low friction method that does not seek to promote sudden changes from one hour to another, Kanban does not provide for changes in roles and responsibilities initially.
The idea is always to have as little impact as possible at the beginning, so that later when problems appear, the team can make the necessary changes.
If one of these identified problems is related to roles and responsibilities, then they should be reviewed and improved. Otherwise, there is no reason to make any changes to the roles.
4) Encourage leadership at all levels
The last principle of Kanban shares the idea that leadership is not a skill exclusive to the highest hierarchical levels in the company.
Every individual can — and should — propose ideas and show leadership in order to Promote Continuous Improvement of the work process.
This principle is fundamental to identifying and promoting changes and adaptations of the flows while encouraging the integration and engagement of the teams.
Reading tip: Psychological Safety: Trust and Inclusion for Innovation and Efficiency
The 4 principles above give rise to 6 core practices to implement Kanban:
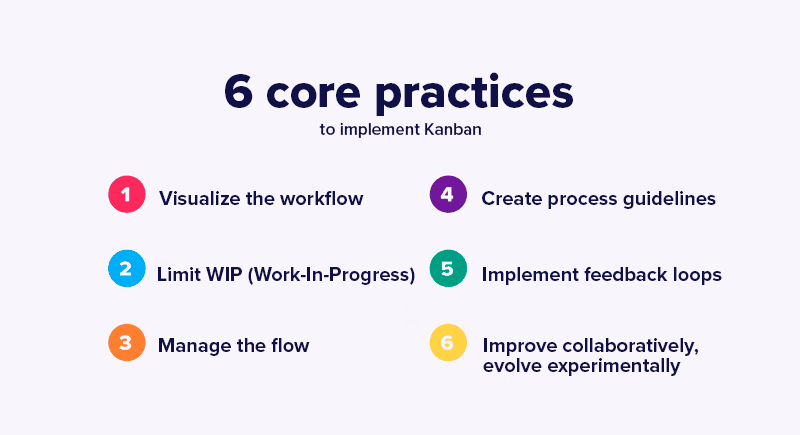
- Visualize the workflow;
- WIP (Work-In-Progress) limit;
- Manage the flow;
- Create process guidelines;
- Implement feedback loops;
- Improve collaboratively, evolve experimentally.
1) Visualize the workflow
Remember that Kanban is a visual tool. Therefore, the first practice to implement it is To be able to visualize the entire workflow on a board, either physical or digital.
Visualizing the workflow makes it easy to see the process, the activities, and the responsibilities of the team involved.
As a rule, the visualization of the flow in Kanban is done from a board, with columns and cards that represent the activities, as shown in the beginning of this article.
2) Limit WIP (Work-In-Progress)
Work-In-Progress refers to the work/activities that are currently being performed. So limiting WIP means setting a number of activities that do not overload teams or individuals.
Kanban works by encouraging teams to finish one activity before they start another. The system gets people to “pull” activities, not to have work pushed onto them.
This practice of WIP limitation, besides helping people to focus, makes it possible to have a vision of the limitations and bottlenecks of the whole process.
3) Manage the flow
The third practice is a consequence of the first two. After building the flow in a visual way and limiting the WIP, it is possible to manage it by understanding the working times of each stage and activity.
From this, it is easy to start Predicting the time for each process and activity, and thus it is possible to create more realistic goals.
Managing the flow means understanding what is happening and making the necessary changes to optimize everyone's work, valuing the deliveries and commitments to the team or company's objectives.
4) Create process policies
Once the workflow is visualized and managed, it starts to make sense to Create guidelines for these processes and activities.
The idea of creating policies is to establish a Guideline of Rules and Practices so that everyone knows what should be done and how it should be done.
Also, policies are a form of communication for new people on the team to understand how the workflow works. Therefore, it is critical that policies are accessible and that everyone is aware of their existence, for consultation and even updates. Common information in process policies includes checklists, SLAs (Service Level Agreements), descriptions of activities, and which roles are involved in each one.
5) Implement feedback cycles
Feedbacks are essential within any process or system and ensure that the work is being done in the best way and that it will be delivered in the shortest possible time.
Kanban, because of its visual characteristics, allows the implementation of several types of feedback, such as:
- final review of activities before the final delivery;
- Communication about difficulties during the process
- communication about opportunities for improvement;
- alignment conversations to remove bottlenecks in the process.
The overriding point of feedback is that it is a process of constant Communication and alignment so that any errors or friction are eliminated as quickly as possible.
6) Improve collaboratively, evolve experimentally
Kanban is a method that allows you to Identify process inefficiencies and promotes the easy and gradual implementation of incremental changes.
With workflow visualization and good management, it is possible to Test Changes without major impacts on the process as a whole.
In this way, we can say that Kanban promotes, in a way, Scientific Thinking, where a hypothesis is established — faced with a question — and it is possible to test the solution possibilities in a controlled manner.
One of the great strengths of Kanban is precisely to promote this constant evolution in a collaborative way, where all people can give ideas and feel engaged in improving their processes.
Reading tip: UX Design — Science or Art?
What are the advantages of the Kanban method?
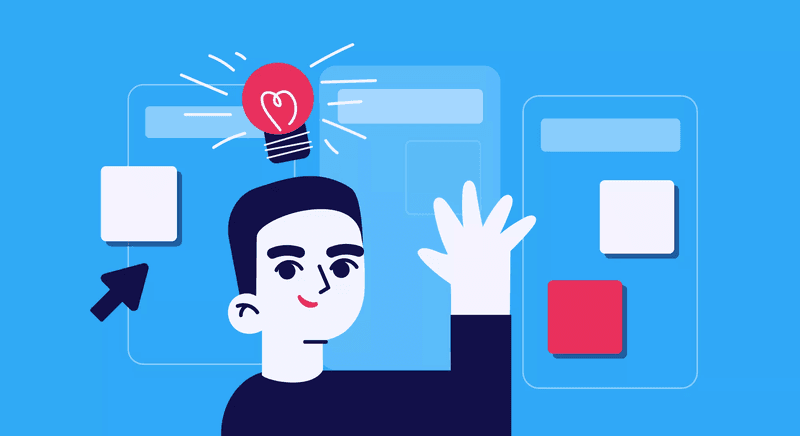
Describing the principles and practices of Kanban gives you an idea of the advantages of adopting this method in processes and workflows.
In this sense, when we list the main advantages of Kanban, we have:
Optimization and improvement of the work process: Due to its visual characteristic, Kanban allows the identification of improvement points in the processes, optimizing the flow and increasing productivity.
Cost reduction: cost reduction with Kanban happens on several levels, either in the better management of materials and stock (as it happened at Toyota) or in the reduction of errors and bottlenecks that can delay deliveries to final customers.
Moreover, work optimization promotes better use of each person's time, reducing overload and possible costs with overtime and even with employees' physical and mental health.
Improved team communication: the practice of constant feedback cycles encourages more efficient and frequent communication between individuals and teams.
In turn, communication is important to identify difficulties, bottlenecks, or discomforts along the workflow and activities.
Task prioritization: because of the WIP limitation and the visualization of the process as a whole, Kanban allows easy identification of priority tasks and activities at the moment.
This issue is important in order not to overload people and to meet the demands in the correct timeframe, without losses.
Kanban in agile environments
Given its characteristics, advantages, and ease of implementation, Kanban is a methodology widely used in environments based on the agile philosophy.
The agile philosophy, in a very succinct manner, is a set of ideas and principles that aim to Optimize the product development flow, providing best practices and iterative cycles for rapid evolutions and improvements.
Therefore, the Kanban methodology fits perfectly in agile environments because of its dynamics, ease of use, and mapping of process bottlenecks and frictions.
Kanban vs. Scrum
Although it is quite common in agile environments, Kanban is not the only tool present in these systems.
scrum is also a methodology often used in conjunction with Agile principles.
The two methodologies are different but may cause some confusion for those who are just starting to use them. Therefore, we will put here the main differences between these methods.
Kanban: is used to visualize the workflow, understand where the bottlenecks are, propose improvements, and optimize the process as a whole. The use of Kanban is not limited to a specific project or time, being a tool of continuous and constant use.
Furthermore, Kanban is easy to implement and does not require changes in roles or responsibilities, or preliminary adaptations.
Scrum: is used in product development projects and is not continuous, working in Sprints that can last up to 4 weeks.
In addition, there are initial preparations that should be taken into consideration before starting to use Scrum. It is important to define Roles and Responsibilities, as well as explain how the method works to all participants.
Therefore, Kanban and Scrum are methods that complement each other within an Agile environment. You don't have to choose between one and the other, because their goals are quite different.